TECH
How a Tig Torch Grip Makes Welding Easier for Everyone
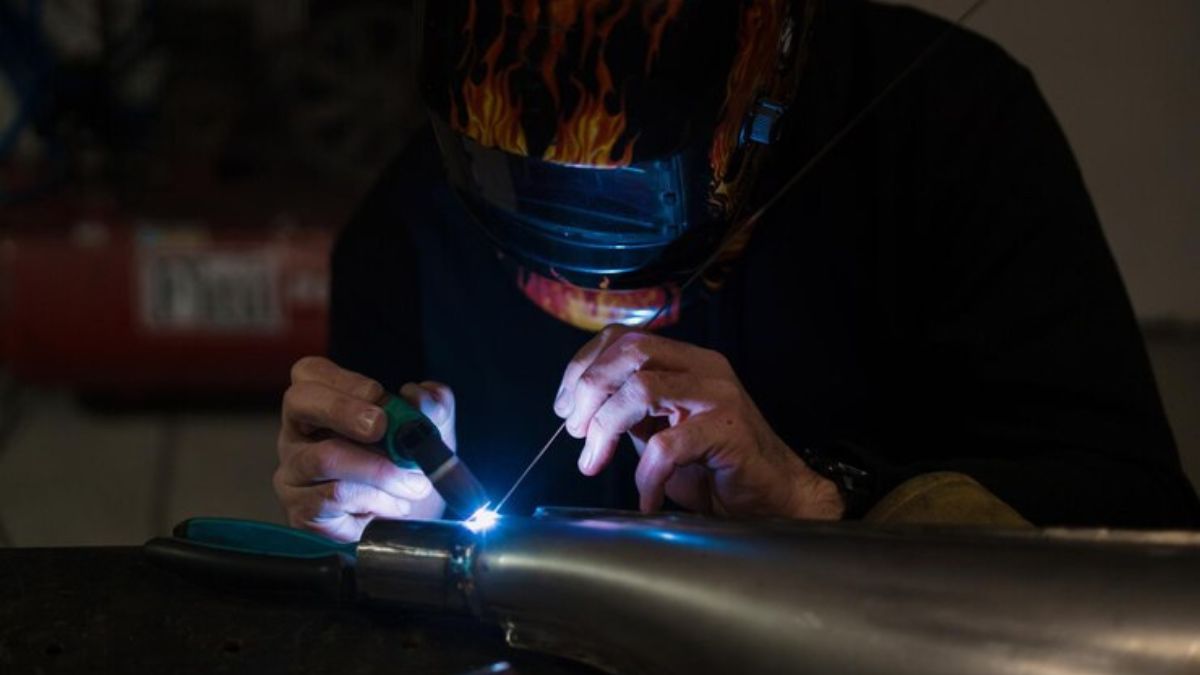
Introduction
Welding, a crucial skill in numerous industries, is both an art and a science. It demands precision, control, and impeccable focus. Tools that enhance dexterity and comfort are invaluable for novices and experienced welders. One such innovation that has gained popularity in the welding community is the Tig Torch Grip. By facilitating better handling and reducing strain, this tool is transforming the welding landscape to be more accessible to everyone.
Enhancing Precision and Control
The Tig Torch Grip is more than just an accessory—it’s a game-changer for precision and control. Its design allows welders to hold the torch comfortably, granting better stability and manipulation of the welding arc. This directly impacts the welds’ quality, as the welder can maintain consistent angles and pressure. Whether welding intricate metal art or constructing robust architectural elements, consistent control leads to better outcomes. This grip can make learning the technique less daunting for beginners, as it aligns with natural hand movements, making them feel more secure and confident during operations.
Reducing Fatigue Through Ergonomic Design
Welding can be physically demanding. Long torch-holding hours lead to hand strain and fatigue, affecting performance and overall output. The ergonomic design of the Tig Torch Grip addresses these challenges by mimicking the hand’s natural grip. This thoughtful design reduces undue strain on the welder’s muscles and joints. As a result, welders can work longer hours with less discomfort, improving productivity and decreasing the potential for errors caused by fatigue. This is particularly beneficial in professional settings where extended work periods are standard.
Stability and Comfort for Quality Results
Quality welding is often determined by the steadiness and precision of the welder’s hand. With a Tig Torch Grip, welders achieve increased stability, which is crucial in producing clean and defect-free welds. The added comfort translates into smoother movements and fewer unintended slips, leading to more uniform weld beads. Consistency in the quality of welds elevates the standard of projects, whether they are intricate sculptures or large infrastructure tasks, ensuring they are built to last and meet rigorous safety standards.
Making Welding More Accessible
The Tig Torch Grip enhances the skills of seasoned professionals and plays a vital role in making welding more approachable for newcomers. Its intuitive design helps reduce the learning curve, enabling amateurs to experience successful welds early in their journey. Removing some physical barriers and challenges, beginners face fosters a more inclusive environment in workshops and learning institutions. As more people find welding accessible, a wider pool of talent and creativity emerges, enriching the industry and inspiring innovation.
Conclusion
In conclusion, the Tig Torch Grip is revolutionizing the welding process by making it more efficient, comfortable, and accessible for all levels of expertise. Its benefits are far-reaching and transformative, from enhancing precision and control to reducing fatigue. As welding continues to be an integral part of multiple industries globally, innovations like these significantly contribute to advancing the craft. Welcoming such developments is crucial as they empower welders of all skill levels to excel, pushing the boundaries of what is possible in metalwork.
TECH
The Role of Engine Cylinder Blocks in Modern Automotive Engineering
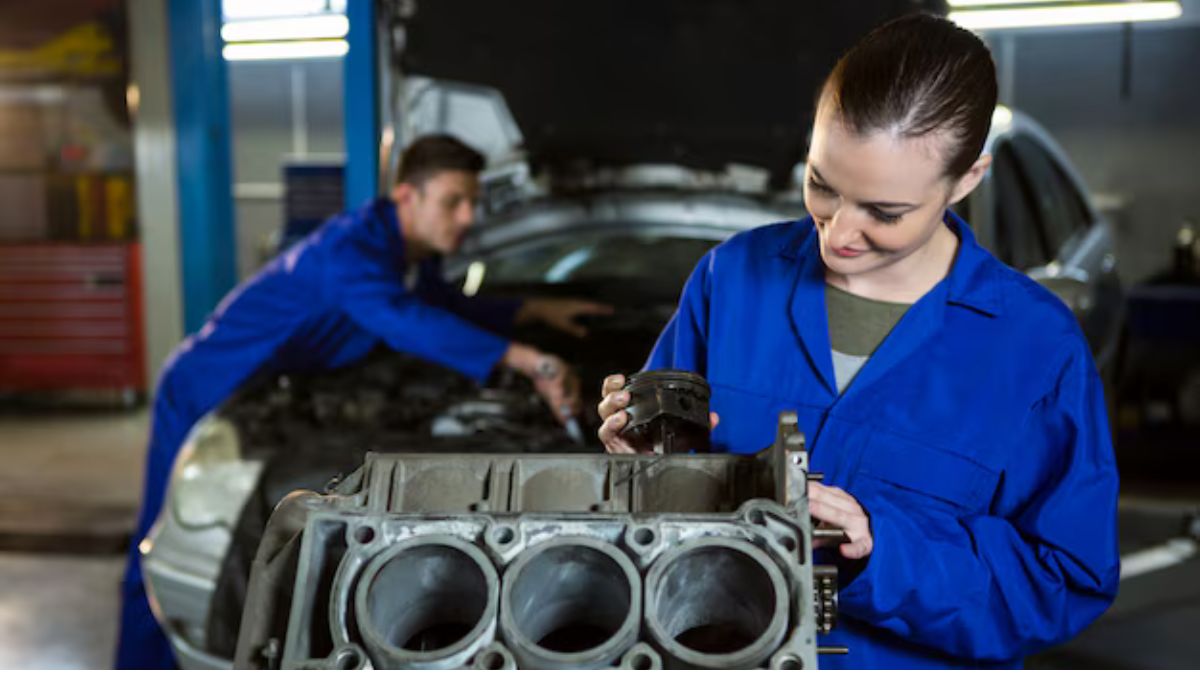
Introduction
The engine cylinder block is the backbone of a vehicle’s engine. Without it, the intricate dance of pistons, valves, and fuel would be impossible. Modern engines rely heavily on the robust design of cylinder blocks to maintain performance and efficiency. Additionally, various components, like cylinder heads Victoria TX, are integral to this system, enhancing the overall functioning of engines. The role of the cylinder block is not just fundamental but also multifaceted, ensuring that the engine runs smoothly under different operating conditions.
This article explores the role, materials, and advancements of engine cylinder blocks in modern automotive engineering, providing insights into their complexities and contribution to engine performance, efficiency, and durability.
What Is an Engine Cylinder Block?
An engine cylinder block is a crucial structural component that houses the cylinders of an engine, providing structural integrity for combustion and piston movement. It serves as the foundation for other engine components like the crankshaft and camshaft, providing mounting points and channels for coolant and oil flow. The design of an engine cylinder block can vary based on the engine type. Still, its core function remains to provide a stable and durable structure capable of withstanding internal forces. Understanding these nuances can help manufacturers tailor engines for specific performance needs.
Importance in Engine Performance
A well-designed cylinder block enhances an engine’s efficiency and performance by absorbing and distributing heat efficiently. It must withstand immense pressure and heat generated during combustion, requiring robust engineering and precise manufacturing processes. Even minor imperfections can significantly affect performance. Precision in manufacturing ensures optimal sealing between the cylinder head and block, enhancing compression and engine efficiency. High-quality cylinder blocks provide excellent thermal conductivity, allowing for quick heat dissipation and maintaining optimal operating temperatures.
Materials Used in Cylinder Blocks
Cylinder blocks are typically made from cast iron or aluminum alloys, with cast iron being durable and withstanding high temperatures for heavy-duty applications. Aluminum is lighter and better at heat dissipation, which is essential for high-performance engines. Research is ongoing to explore alternative materials like magnesium and advanced composites for improved strength-to-weight ratios. The choice of material also impacts the manufacturing process and production cost. Cast iron offers robustness but can affect vehicle weight and fuel efficiency. Aluminum alloys, although more expensive, balance durability and weight, making material selection crucial for manufacturers to meet different vehicle application demands.
Manufacturing Processes
The manufacturing of engine cylinder blocks involves several complex processes, including casting, machining, and inspection. Melted metal is poured into a mold during the casting process to create the fundamental geometry of the block. After cooling and solidifying, the block undergoes machining to achieve the precise dimensions required. Finally, each block is inspected for defects and imperfections to ensure it meets stringent quality standards.
Advances in manufacturing technology have enabled more efficient and precise production of cylinder blocks. Techniques like high-pressure die casting and CNC machining have revolutionized the industry, allowing for the creation of complex geometries with high precision. Quality control measures, including ultrasonic testing and X-ray inspection, ensure that each cylinder block meets the required standards of strength and durability.
-
TECHNOLOGY9 months ago
Top 5 Tips for Mastering in_a_dndmixin_drag in Your Campaigns
-
TOPIC8 months ago
Exploring the History and Culture of Rosewellsk
-
TECHNOLOGY9 months ago
YMoviesHD vs Other Streaming Platforms: A Comprehensive Comparison
-
TOPIC9 months ago
Behind the Scenes: The Philosophy and Vision of PhmHaven
-
TOPIC9 months ago
The Rise of Tribute Printed Pics: Honoring Life Through Photography
-
TOPIC8 months ago
A Beginner’s Journey with Lwedninja: From Novice to Pro
-
TOPIC8 months ago
Is Finizona Free? Unpacking the Costs Behind This Popular Platform
-
TOPIC8 months ago
Decoding m0therearf: Why This Buzzword Matters in Today’s Culture